Fabrication, Manufacturing & Assembly
As The Old Adage Says, “Measure Twice, Cut Once.”
The concept of accuracy being of ultimate importance has come sharply into focus in the modern world of HVAC design, manufacturing and installation. Helm is committed to the earliest practical adoption of technology in every one of our divisions and HVAC/Mechanical manufacturing is no exception. With 160,000 square feet of fabrication, modularization and assembly shop space, the future of advanced HVAC manufacturing is alive and well at Helm today. While high-level Building Information Modeling (BIM) and advanced manufacturing techniques are talked about by many contracting companies, few can fully execute because it requires a dauntingly high level of capitalization and commitment to infrastructure, software and talent development.
The technological hub of Helm’s Rockford Fab Shop are two state of the art pieces of advanced manufacturing automation: our top-shelf Bescutter Fiber Laser Cutter and Iowa Precision Coil Line Duct Former.
Because its beam is more readily absorbed and not reflected, fiber laser cutters cut copper, brass and aluminum better, more efficiently and more safely than CO2. And, fiber laser operating costs are lower thanks to more modest electrical consumption. Fiber laser cutting is used in many industries where low tolerances are the name of the game – including in medical center operating rooms all over the world. We are proud to bring the precision, repeatability, speed and automation of today’s most accurate contactless cutting to our customers’ projects.
Helm’s sheet metal shop is centered around a Duct Former Coil Line with 5 coil feeds and liner capability. The coil line manufacture duct to SMACNA-quality standards with repeatable precision.
Our Hydraulic Plate Roller is another key automation hub in Helm’s advanced manufacturing system that feeds, sequences and forms nearly all duct sizes and shapes from pre-programmed data entries. Our hydraulic machinery forms and joins full-wrapper duct quickly, accurately and less expensively than less-advanced, less-automated equipment. Helm’s plate rolling equipment is fully integrated via automated tooling and software by our design engineers for seamless, incredibly accurate and dependable data transfer.
In Helm’s pipe fabrication shops, Helm uses Tigerstop equipment to automate the pipe cutting process and large pipe is cut on a Watts cutter using the latest plasma technology. In addition to the fabrication of any piping material, we build complex steel structures for our projects and outside customers. One noted example of our structural steel capabilities, was the manufacture of the structure for the famed Daniel Inouye Telescope in our Freeport, Illinois shop. The world’s largest solar telescope was then dis-assembled and shipped to Maui for final installation.
All assemblies are tracked in Stratus, our quality control and process management system. Helm’s 12 weld booths, stand-alone bioprocessing equipment, orbital weld shop and expert pipe support assembly provide cutting edge resources to our field work.
Modularization planning begins at the earliest stages of each and every Helm project in conceptual design meetings. In close collaboration with project partners, we identify the most efficient solutions for each and every project. Coupled with our state-of-the-art automated tooling and software packages (some of which were beta-tested at Helm), the Helm Project Team utilizes BIM to extract and leverage information for use in the planning and delivery of the offsite prefabrication modules as well as all other logistics planning for site deliveries and installation. Prefabrication eliminates waste onsite and provides “just in time” delivery of pre-fabricated assemblies. That further enhances site safety and efficiency, reduces waste and generates higher quality. The real benefits of prefabrication all come together in pipe and duct systems that are all but fully assembled at our Fab Shops, then shipped for lightning-fast, accurate assembly at our job sites. To learn more about how Helm’s prefabrication expertise can benefit your next project, please send us an email. We will respond promptly.
Our Advanced Manufacturing Solutions Include
- State-of-The-Art Automated Fiber Laser Cutting Equipment
- ASME “PP” Stamp
- “R” Stamp Certification by the National Board
- State-of-The-Art Automated Pinch Rolling Plate steel Manufacturing
- Leading Edge Design & Manufacturing Software and BIM Integration
- 160,000 Square Feet of Fabrication Facilities
- BPE (Bioprocessing Equipment Shop)
- Full Duct Shop Capabilities including Duct Line
- Metal fabrication for industrial exhaust systems
- Architectural metal capabilities
Our Defining Centers Of Excellence
- Innovation & Early Adoption Of The Finest Technology
- Enduring Commitment to Building Information Modeling
- Highest Standards for Quality Control & Craftsmanship
- 24/7 Service
- Long-Tenured, Talented Management Team
- Decades of Experience Dating Back To 1969


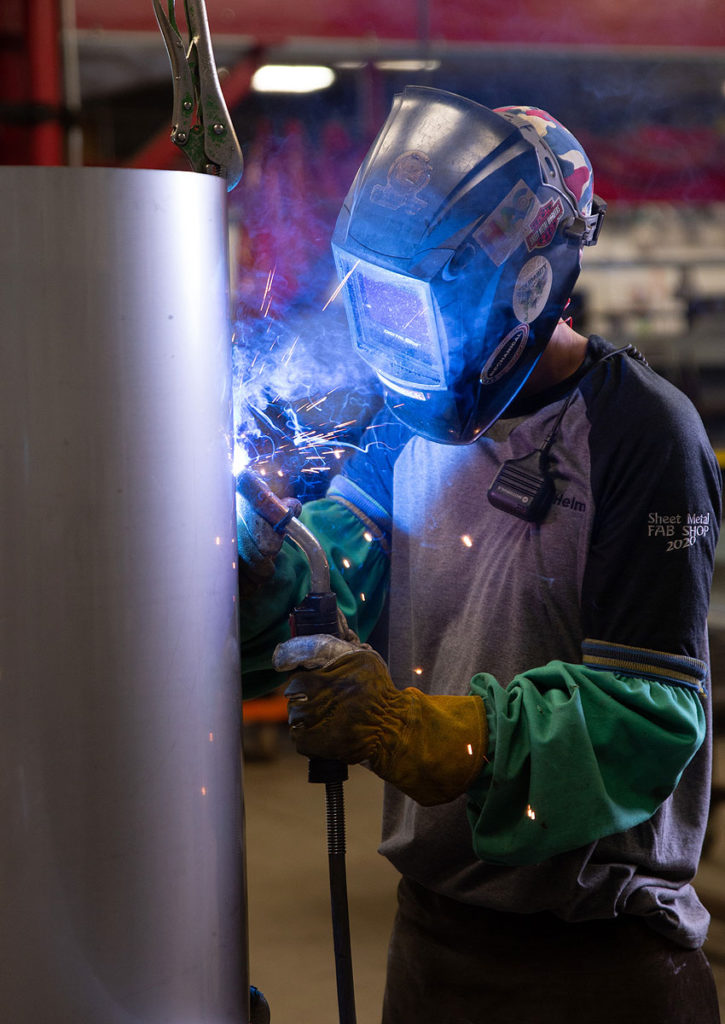

